Why technology is fallible
Growth in the use of CAD/CAM systems continues to gain in popularity, and it is easy to see why. It is generally sold as a quick easy method to create anything you desire. Well, that’s not quite true, says APPLE NOOTENBOOM
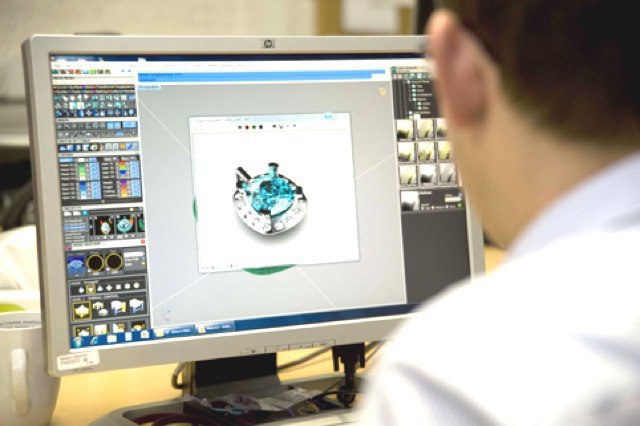
I have previously raised the issue of poor technical/structural design consideration, but this time I want to raise the issue of failings in the technology systems themselves, or is it the operatives?