Saying ‘Yes’ to platinum
For the jewellery industry, a striking feature of the recession years has been the resilience of platinum. The Birmingham Assay Office’s SARAH DEVERELL explains some of the science behind this top-end metal.
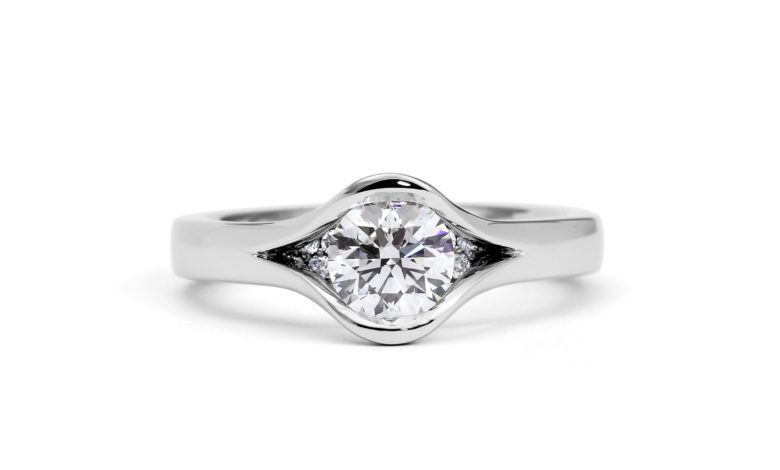
Platinum has been successfully marketed as the ultimate precious metal and has proved relatively resilient to recent financial turmoil. Volume in the platinum market is very much driven by the bridal market and it has fared slightly better than gold and silver.