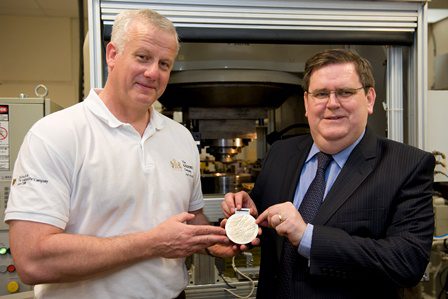
Legal reasons had prevented the organisation from announcing its hallmarking of the medals prior to the Games.
Join 5,000 jewellery professionals with a membership
Get unlimited access and stay in the know. First-year special offer pricing. Cancel any time.
You'll need to subscribe to continue.
How many members should have access to the subscription?
Monthly
Yearly
Save £9.89
No, thanks
I already have an account
Legal reasons had prevented the organisation from announcing its hallmarking of the medals prior to the Games.